Understanding Metal Lathe Machine Parts: A Comprehensive Guide
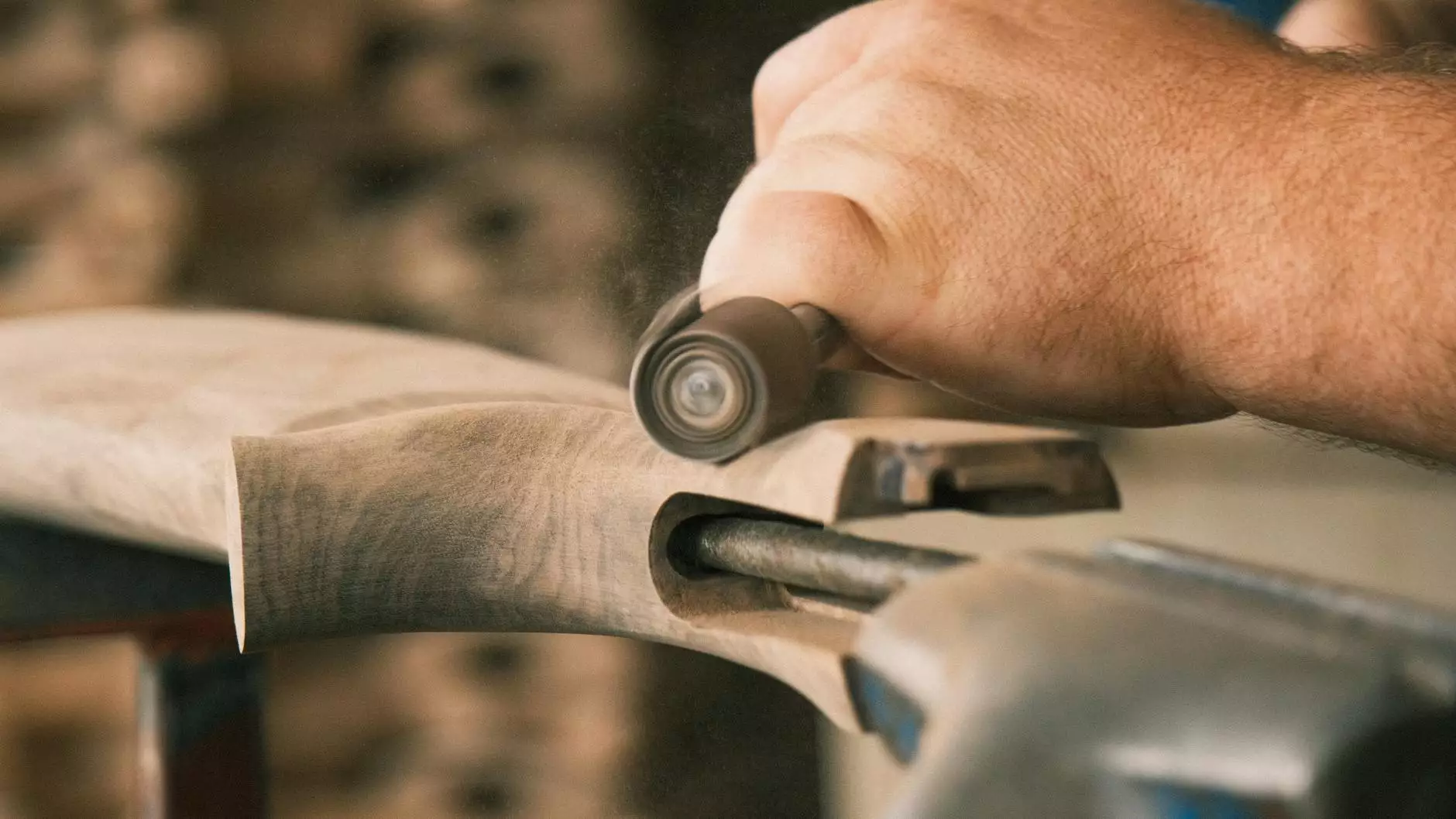
In the world of precision manufacturing, metal lathe machine parts hold a pivotal role. These components are not just integral to the operation of lathes; they are fundamental to ensuring high-quality production standards in various industries. This extensive article delves deep into the critical parts of metal lathe machines, emphasizing their importance, functionality, and maintenance practices.
The Essence of Metal Lathe Machinery
Metal lathes are among the most versatile tools in the machining arsenal, utilized for shaping and cutting metal. The functionality of these machines heavily relies on the precision and quality of their parts. Each component serves a distinct purpose, working in harmony to create intricate designs, prototypes, and finished products.
Core Components of Metal Lathe Machines
Understanding the metal lathe machine parts is crucial for anyone involved in machining or metalworking. Below, we explore the primary components that make up these machines:
1. Headstock
The headstock is the powerhouse of the lathe, housing the main motor and providing the speed for the spindle. It includes several vital parts such as:
- Spindle: Connects to the motor and is responsible for rotating the workpiece.
- Speed Control: Allows operators to adjust the spindle speed for different materials and applications.
2. Tailstock
Opposite the headstock, the tailstock supports the other end of the workpiece. It can be adjusted along the length of the lathe and contains:
- Quill: A retractable cylinder that holds tools for drilling, boring, and reaming.
- Locking Mechanism: Ensures the quill remains secure while in use, preventing any unwanted movement.
3. Carriage
The carriage is responsible for moving the cutting tool across the workpiece. It consists of several parts:
- Cross Slide: Moves perpendicular to the workpiece, allowing the tool to make precise depth cuts.
- Compound Slide: Enables angular adjustments for tapered cuts, increasing flexibility.
- Tool Post: Holds the cutting tool firmly in place, ensuring stability during operation.
4. Bed
The bed is the foundation of the lathe machine, providing support and alignment for other parts. It must be made from durable materials to withstand the forces exerted during machining operations. Key attributes include:
- Stability: Essential for precision, preventing vibrations that could lead to poor-quality work.
- Alignment: Critical for the accuracy of the lathe, ensuring all parts work in synchrony.
5. Apron
The apron is an essential part of the carriage that allows the operator to control movements manually. It includes:
- Handles: For manual adjustments and tool movements.
- Gears: Facilitate easy and controlled movement across the latitude of the bed.
Importance of Quality Parts in Metal Lathes
The quality of metal lathe machine parts directly influences the overall performance of the lathe. Using high-grade materials and precision engineering ensures:
- Increased Longevity: Robust components resist wear and tear, leading to prolonged machine life.
- Improved Precision: Accurate parts facilitate tighter tolerances, essential for high-quality production.
- Enhanced Performance: Quality components minimize downtime and improve operational efficiency.
Common Materials Used in Metal Lathe Parts
The materials chosen for constructing metal lathe machine parts are fundamental in determining durability and performance. Some commonly used materials include:
1. Cast Iron
Widely utilized due to its excellent dampening properties and stability, cast iron is a preferred choice for lathe beds. Its innate ability to absorb vibrations leads to better machining outcomes.
2. Steel
High-carbon steel is often used for parts that require strength and resilience. Components such as spindles and cutting tools are frequently made from steel due to its hardness and ability to retain sharp edges.
3. Aluminum
Aluminum parts are gaining popularity for their lightweight nature and corrosion resistance, making them ideal for certain components of the lathe.
Maintenance Tips for Metal Lathe Machine Parts
Regular maintenance of metal lathe machine parts is essential to ensure optimal performance and longevity. Here are some effective maintenance practices to consider:
1. Regular Lubrication
Keeping all moving parts adequately lubricated reduces friction and wear. Use the recommended lubricants for each component to maintain smooth operations.
2. Securely Tightening Components
Periodically check and tighten screws, bolts, and other fastening devices to prevent loose components that could impair machine functionality.
3. Cleanliness
Keep the lathe clean from debris, shavings, and dust. A clean machine runs more efficiently and helps in identifying wear and defects in parts early on.
4. Regular Inspections
Conduct routine inspections for signs of wear or damage. Addressing issues promptly can prevent major repairs and downtime.
The Future of Metal Lathe Machine Parts
The evolution of technology is continuously influencing the design and functionality of lathe machine parts. Innovations such as:
- CNC Technology: Computer Numerical Control (CNC) lathes allow for automated operations, significantly increasing productivity and precision.
- Advanced Materials: The introduction of composite materials promises lighter, stronger, and more durable components.
- Smart Technology: Integration of IoT devices for predictive maintenance can ensure machines operate at peak efficiency while minimizing downtime.
Conclusion
In conclusion, understanding the intricacies of metal lathe machine parts is essential for anyone involved in machining. From the headstock to the tailstock, each component plays a vital role in ensuring the efficacy and precision of the manufacturing process. By maintaining high-quality parts and embracing emerging technologies, businesses can significantly enhance their production capabilities.
For more detailed insights and top-notch metal lathe machine parts, visit our website at deepmould.net. Equip your shop with the best components and ensure your lathe operations are top-tier!